__________________________________________________________________________________________________________________
__________________________________________________________________________________________________________________
Bau der Leitwerke
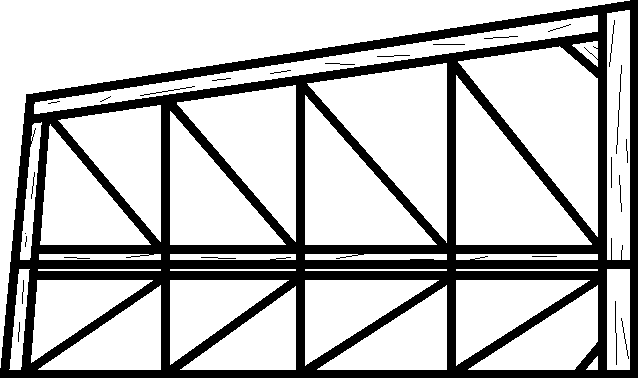
Die Aufrisse der Leitwerke habe ich mir maßstäblich
ausgedruckt und als Bauunterlage
verwendet.
Für alle Endleisten der Leitwerke, habe ich 1,5 mm
Kohlerundstäbe verwendet.
Für die Flächen und deren Querruder 3 x 1 mm
Kohleflachstäbe.
Diese, mit etwa 25mm langen Kohlerovings und Sekundenkleber zu
den
Rippen und Stegen verstärkt und verbunden.
Hierbei die Rovings mit einem stück PVC-Folie bis zur relativ
schnellen
Aushärtung angedrückt.
Dies geht geht verhältnismäßig schnell, ist einfach,
sehr haltbar und von
geringen Gewicht.
Die Bespannung, mit 15g/m² - Papier und darauf ein 19g/m² -
Polyestergewebe
(Chiffon) mit Spannlack der großen Fliegerei,
ergibt eine extrem feste, kompakte und haltbare Bespannung.
Selbstverständlich muss das Holz mit einem ausreichenden Anstrich
mit
Porenfüller oder Spannlack vorbehandelt werden,
um das typische Aufquellen bei der Aufbringung des Papiers mit
Dispersionsleimen zu verhindern.
Das Papier erhält durch das Gewebe eine enorme straffe Festigkeit
und lässt
keinen Spannlack durchtropfen.
Auch bei diesem Modell habe ich die Flächen und Leitwerke (wo
möglich) in einem
Stück bespannt und dieses gleichzeitig als Scharniere verwendet.
Diese gehen sehr leicht, sind haltbar und auch Spaltfrei
(Luftundurchlässig = kein Druckausgleich).
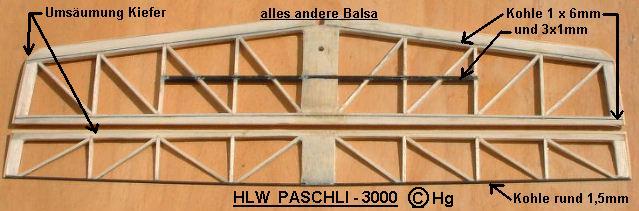
Hier, das für die Bespannung
rohbaufertige Seitenleitwerk.
Die Profilierung ist oben, unter den Techn.- Daten abgebildet.
Die Trennung des Ruders vom Leitwerk geschieht erst nach der fertigen
Bearbeitung mit Schleifbrettern mit
der anschließenden Anleimung der Kiefernleiste am Ruderflap.
.Nur
so ist eine sehr gute Passgenauigkeit mit einem geringen Aufwand
möglich.
Das gleiche Verfahren habe ich beim Bau des SLW angewendet.
. . . . . . . . . . . . . .
Bilder SLW Hier die Abbildung
des SLW in 2 Bauschritten.
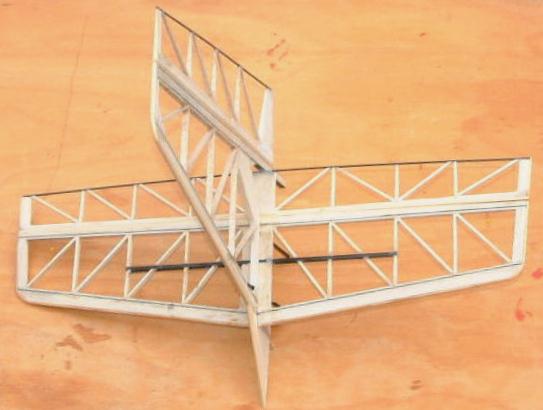
Fertig vor der Bespannung, Zusammenbau und Anbau an
den Leitwerksträger. Trennung der Ruder erst nach dem
Feinschliff !
Die Klebungen an den Leitwerken habe ich fast ausschließlich mit billigen Sekundenkleber gemacht.
Rohbaugewicht 48g mit den
Kohlerohren für den stabilen Anbau an den LW-Träger/Rumpf.
================================
Rumpfbau
Bild
R1
Hier
in Bild 1 die Rumpfkeule eines sehr preiswerten
Cliff-Hawk
von Michael
Beineke/36129 Gersfeld, den ich noch
so herum liegen
hatte, dessen Leitwerksträger für das Modell aber zu kurz
war, deshalb
abgetrennt wurde, und mit einem längeren und stabileren
Leitwerksträgerrohr versehen wurde. Siehe hier,
aus Kohle- und Kevlarschläuchen laminiert. Für eine
größere Steifheit, Festigkeit, habe ich ihn getempert.
Die
Rumpfkeule wurde mit einem Kohleband und einer Lage
200g Glasgewebe zusätzlich verstärkt. Die Kohlebänder
aber nur bis kurz hinter
der Haubenöffnung, unter das Glasgewebe eingelegt, da der
Kohleschlauch des
Leitwerkträgers als Antenne verwendet wird. Der rote
Antennenanschlussdraht am Leitwerksträgerrohr ist
in den Bild R2 gut erkennbar.
Bild R2
Bild
2
Am
Leitwerksträger ist der Schlauch zur besseren Ausrichtung bei der
Einklebung
wie ein Besen auseinander gespreizt der dann noch angepasst werden
muss.
Die
spätere Eintauchtiefe des Leitwerkträgers ins Rumpfboot
ist in etwa der
Darstellung gleich. Die Einschnitte am Ende des Rumpfbootes
ermöglicht
eine bessere Anpassung an den Durchmesser des Leitwerkträgers.
Etwas mit dem
Heißluftfön erwärmt, ergibt eine bessere Anformung.
Bild R3
Bild R4
Bild
R3
zeigt das bearbeitete,
angepasste
Rohrende für die
Einklebung . Bild R4
zeigt
das passend für die Klebung eingeschnürte Bootsende.
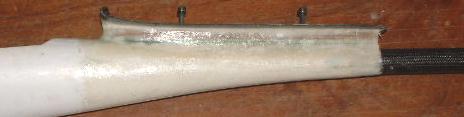
Bild
R5
Bild R
In
Bild 5 und Bild6 (vor der Lackierung) der angebaute
Pylon mit der
Flächenbefestigung. Es werden 4 Innensechkantschrauben
verwendet, die in Schlagmuttern geschraubt werden. DerPylon ist aus
einem 9mm Multiplexsperrholz gefertigt und dieses mit 4 M3
Stahlschrauben und Muttern am Rumpf befestigt. Mit Harz und
Mikroballons
unterfüttert/verklebt und angeformt. Dann nach den
Anschleifen/Verschleifen mit 60g Glasgewebe/Harz überzogen. Die
Flächenauflage ist mit Kohle-
und Glasgewebe über die zusammengebauten Flächen geformt
worden, um eine passgenaue Auflage zu bekommen.